||
Looking for a way to boost productivity and increase revenue in your business? Of course you are. Who isn’t? But how can you reach those goals without making major changes and spending lots of your hard-earned capital? Focus on reducing idle time within the workflow.
At first glance, idle time may not seem like it’s having a large impact on your bottom line, but even a few minutes here and there can quickly add up over the course of a year and cost your business hundreds, if not thousands, of dollars in lost profit.
But what exactly is idle time? How can you calculate it? And, once you know how much idle time is going on in your business, how can you reduce it? Learn the answers in this article.
Table of contents
- What is idle time?
- How to calculate idle time
- How to reduce idle time
What is idle time?
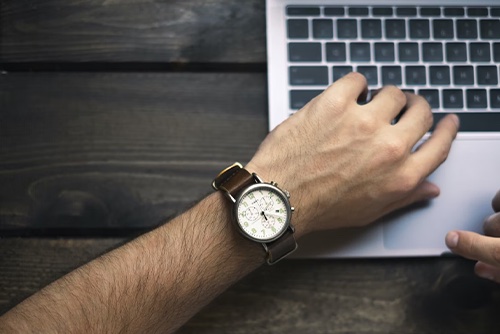
Idle time is defined as:
A period of seconds, minutes, or hours during paid working hours when an employee, a team, a machine, or some other part of a business is unproductive.
While many managers immediately jump to the conclusion that idle time is the fault of employees (e.g., taking unauthorized breaks), much of the blame is actually due to speed bumps in the workflow and policies and procedures that don’t mesh well.
Examples of idle time include:
- Employee A waiting for employee B to unload necessary supplies that just arrived
- Team members waiting on instructions before they can start work
- Lagging equipment
- Power outages
- System failures
- Process inefficiencies
- Waiting for the copier to warm up
- Waiting for large files to download and open
And that’s just the tip of the iceberg.
For businesses that manage a fleet of vehicles, idle time can literally mean the minutes — or even hours — that an engine is idling without some productive movement. Such idling can increase fuel costs to the point that it negatively affects your bottom line.
As you can see, idle time can take many forms and extend beyond the walls of your business.
The good news is that in the vast majority of cases, you can take steps to reduce — or even eliminate — idle time so that your workflow is as efficient and productive as possible.
We’ll discuss ways to reduce idle time later on in this article. But first, we’ll run through a simple way to calculate this variable so you know how it’s impacting your business.
How to calculate idle time
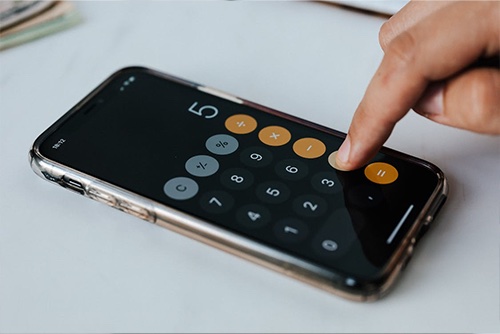
Calculating idle time can get a bit murky when tracking an employee’s work time, so before we tackle that, let’s look at a simpler example: tracking a machine’s work time.
This will give you a more straightforward introduction to the overall calculation.
Machine idle time
Here’s the formula we’ll use:
Idle Time = Scheduled Production Time – Actual Production Time
Let’s say that you’ve scheduled a machine to run for eight hours (its Scheduled Production Time).
But the machine doesn’t go from off to on in the blink of an eye at the start of the day (it takes 15 minutes to get up to speed). Nor does it go from on to off right away (it takes five minutes to power down).
Plus, said machine needs to be turned off for 20 minutes every four hours for cleaning and maintenance (including the five-minute power down and the 15-minute power up).
All of these factors contribute to the Actual Production Time.
So, the Actual Production Time variable is the Scheduled Production Time minus the sum of all the “delays” that reduce productivity.
In our example, those delays are:
- Power up: 15 minutes
- Power down after four hours: 5 minutes
- Cleaning: 20 minutes
- Power up: 15 minutes
- Power down at end of day: 5 minutes
When you add those numbers together, you come up with a full hour when your machine isn’t productive in some way.
In this case, your Actual Production Time is seven hours (Scheduled Production Time – Delays In Productivity). Plug that into the equation, and you get:
Idle Time = 8 hours Scheduled Production Time – 7 hours Actual Production Time
Idle Time = 1 hour
With that number in mind, you can then start to look for ways to cut down on the delays that reduce productivity (e.g., replace an old machine with one that powers up faster).
Employee idle time
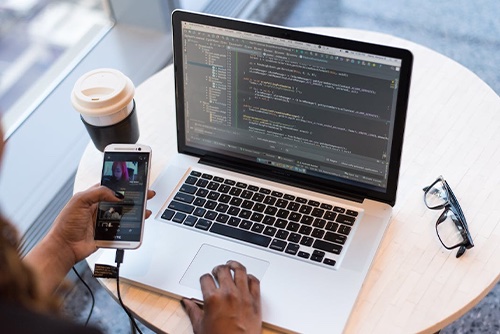
Employee idle time operates on the same principle as machine idle time, but you may have more opaque variables to contend with because employee labor isn’t always as cut-and-dry as machine run time.
An employee may slow down or speed up for reasons you can’t control and may need short breaks more often because they didn’t sleep well the night before.
So, while they may clock in for an eight-hour shift, they may only be productive for seven hours and 15 minutes. That’s a little over five-and-a-half minutes lost every hour (and isn’t really all that bad of an idle time).
You may be able to reduce that number a little bit, but it’s unrealistic to think that you can reduce idle time all the way down to zero.
However, while 100% productivity may not be feasible, you can shave seconds, and even minutes, off a given workflow with a healthy dose of analysis and a bit of hard work. And over time, those minutes will add up. Let’s take a look.
How to reduce idle time
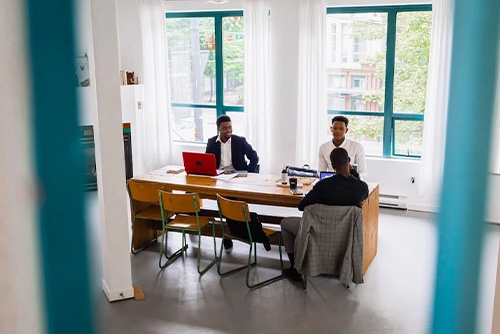
1) Define idle time for your business
As we mentioned, it’s not always realistic to push idle time down to zero. Your business may allow for 7.5 hours of actual production time within an eight-hour shift and not consider that 30 minutes as idle time.
That’s why it’s important to define idle time for your business.
Perhaps a realistic goal for your team is 7.25 to 7.5 hours of productivity per shift. In that case, your definition of idle time might be anything that exceeds 45 minutes of lost productivity not caused by machine failure or some other extenuating circumstance.
2) Ask your team for suggestions
One of the best ways to reduce idle time is to ask your team for suggestions. They’re working on the front lines every day and are intimately familiar with the workflows involved.
Your team may see ways to save time on repetitive activities that you, as management, might not realize are there.
3) Analyze and optimize workflow
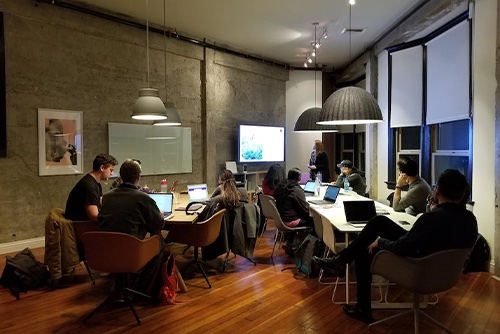
Another excellent way to reduce idle time in your business is to analyze your workflow and then take steps to streamline and optimize the processes involved. A big part of such an analysis is tracking each employee’s time on task.
Knowing how long it takes someone to perform a specific job (e.g., retrieving supplies from inventory) can help you come up with ways to make that task easier and reduce the time it takes to complete.
4) Improve communication
Unclear communication of any kind can have a dramatic effect on productivity. If your employees are confused about when, where, why, and how to do something, it’s going to take them longer to get the job done — assuming they even do it correctly the first time through.
Improving communication — be it written or verbal — goes a long way toward providing your team with the accurate information they need to avoid bottlenecks and delays.
5) Maintain equipment
Maintaining your equipment so that it’s in good repair and runs efficiently all the time is another way to increase productivity in your business.
If a production machine, motorized vehicle, or hand-held tool breaks down, your team is going to have to spend time either fixing it or getting a new one. Such breakdowns are, in most cases, avoidable with a little bit of preventative maintenance.
For example, taking a large production machine offline for a half-hour every few weeks for cleaning and minor repairs can prevent a major breakdown that could last for several days.
Reduce idle time with the right tools
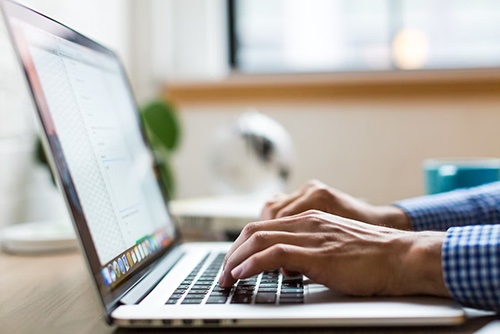
Want to get started reducing idle time right away? Keep your team’s scheduling and task management as tight as possible.
Sling is a powerful suite of tools built to help streamline and optimize your business’s workforce management efforts so that it all runs like a Swiss clock.
Try Sling for free and discover just how easy it is to reduce idle time in your operation and keep your business on the road to success.
For more resources to help you manage your business better, organize and schedule your team, and track and calculate labor costs, visit GetSling.com today.
The post How To Calculate and Reduce Idle Time in Your Business appeared first on Sling.
||----------------------------------------------------------------
By: Sling Team
Title: How To Calculate and Reduce Idle Time in Your Business
Sourced From: getsling.com/blog/idle-time/
Published Date: Tue, 20 Sep 2022 08:11:00 +0000
Did you miss our previous article...
https://coachingbusinessowners.com/growth/subway-ran-a-sandwich-subscription-promotion-and-customers-ate-it-up